The Essential Guide to Control Cable Connectors
Introduction
Control cable connectors are vital components in various industries, including manufacturing, automation, aerospace, and telecommunications. These connectors play a crucial role in establishing reliable connections between control cables and devices, ensuring smooth and efficient operation of complex systems. In this comprehensive guide, we will explore the different types of control cable connectors, their applications, key features, and best practices for selection and installation.
Understanding Control Cable Connectors
Control cable connectors serve as the interface between control cables and equipment, facilitating the transmission of signals, power, and data. These connectors are designed to withstand harsh environmental conditions, ensure secure connections, and provide ease of installation and maintenance. By choosing the right control cable connectors, engineers and technicians can optimize the performance and reliability of control systems.
Types of Control Cable Connectors
There are several types of control cable connectors available in the market, each designed for specific applications and requirements. Some of the most common types of control cable connectors include:
1. Circular Connectors: Circular connectors are widely used in industrial applications due to their robust construction and secure locking mechanism. These connectors are available in various sizes and configurations, allowing for easy installation and maintenance.
2. Rectangular Connectors: Rectangular connectors are commonly used in electronic devices and control panels where space is limited. These connectors offer high contact density and are suitable for applications requiring high-speed data transmission.
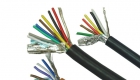
3. D-Sub Connectors: D-Sub connectors, also known as D-Subminiature connectors, are popular in the computer and telecommunications industries. These connectors feature a D-shaped metal shell and are available in different configurations, including DB9, DB15, and DB25.
4. Coaxial Connectors: Coaxial connectors are used for RF and microwave applications where precise impedance matching is critical. These connectors feature a central conductor surrounded by a dielectric insulator and an outer conductor, providing excellent shielding and signal integrity.
5. Fiber Optic Connectors: Fiber optic connectors are used for high-speed data transmission over long distances. These connectors utilize optical fibers to transmit data through light signals, offering high bandwidth and immunity to electromagnetic interference.
Applications of Control Cable Connectors
Control cable connectors find applications in a wide range of industries and systems, including:
1. Industrial Automation: Control cable connectors are essential for connecting sensors, actuators, and control devices in automated manufacturing processes. These connectors enable real-time communication and control, improving efficiency and productivity.
2. Aerospace and Defense: Control cable connectors are used in aircraft, spacecraft, and military systems to establish reliable connections between avionics equipment and control panels. These connectors must meet stringent requirements for performance, reliability, and safety.
3. Telecommunications: Control cable connectors are vital in telecommunications networks for connecting fiber optic cables, coaxial cables, and control systems. important site ensure seamless communication and data transmission across different network components.
4. Medical Devices: Control cable connectors are used in medical devices and equipment for transmitting signals and power between sensors, monitors, and control units. These connectors must meet medical safety standards and requirements for patient care applications.
Key Features of Control Cable Connectors
When selecting control cable connectors for a specific application, it is essential to consider the following key features:
1. Connector Type: Choose the appropriate connector type based on the requirements of the system, such as circular, rectangular, D-Sub, coaxial, or fiber optic connectors.
2. Contact Configuration: Consider the number and arrangement of contacts in the connector to ensure compatibility with the cables and devices being connected.
3. Environmental Protection: Select connectors with adequate sealing and shielding to protect against dust, moisture, vibration, and electromagnetic interference.
4. Operating Temperature Range: Choose connectors that can operate within the specified temperature range of the application to ensure reliable performance in extreme conditions.
5. Mounting Style: Consider the mounting options available for the connector, such as panel mount, PCB mount, or cable mount, based on the installation requirements.
6. Locking Mechanism: Ensure that the connector features a secure locking mechanism to prevent accidental disconnection and maintain signal integrity.
7. Durability and Reliability: Select connectors with robust construction and high-quality materials to withstand frequent mating cycles and harsh environmental conditions.
Best Practices for Selection and Installation
To ensure optimal performance and reliability of control cable connectors, follow these best practices for selection and installation:
1. Identify Application Requirements: Understand the specific requirements of the application, including signal type, voltage, current, frequency, and environmental conditions, to select the most suitable connectors.
2. Consider Future Expansion: Choose connectors that allow for future system upgrades and expansions to accommodate changing requirements and technologies.
3. Follow Manufacturer Recommendations: Refer to the manufacturer's specifications and guidelines for selecting compatible connectors and ensuring proper installation and operation.
4. Perform Proper Cable Preparation: Strip and terminate the control cables according to the connector manufacturer's instructions to ensure secure and reliable connections.
5. Use Proper Tools and Techniques: Use appropriate tools and techniques for crimping, soldering, or terminating connectors to avoid damage and ensure proper electrical continuity.
6. Conduct Testing and Validation: Test the installed connectors for continuity, insulation resistance, and signal integrity to verify proper functionality before putting the system into operation.
7. Follow Safety Guidelines: Adhere to safety precautions and guidelines when handling control cable connectors to prevent injury or damage to equipment.
Conclusion
Control cable connectors are essential components in various industries and systems, providing reliable connections for transmitting signals, power, and data. By understanding the different types of connectors, their applications, key features, and best practices for selection and installation, engineers and technicians can ensure the optimal performance and reliability of control systems. Choose control cable connectors carefully, follow recommended installation practices, and conduct regular maintenance to maximize the lifespan and efficiency of your systems.